Cut Edge Corrosion: Treatment, Repair and Protection For Metal Roofing
Cut Edge Corrosion UK, specialise in delivering superior cut edge corrosion treatment and corrosion control services across the UK. Our extensive range of services include; cut edge corrosion treatment, roof restoration, metal roof maintenance, and the application of protective coatings. Guided by our commitment to provide our customers “The Edge In Corrosion Control”, we utilise advanced techniques and high-quality roof coating systems to ensure industrial and commercial roofs remain resilient and well-protected. With a strong focus on customised solutions and meticulous attention to detail, we handle every project with the utmost care, safeguarding your property for the long term. Trust Cut Edge Corrosion UK for exceptional service and unparalleled protection against corrosion.
Cut edge corrosion is the deterioration of exposed metal edges, typically found on sheet laps or sheet ends of profiled metal roof panels or cladding. Cut edge corrosion issues develop due to the protective coating of metal roof sheets being cut during the installation process. Over time this protective coating begins to peel. Once coating peel starts, the metal sheet edge beneath the protective coating is exposed to the environment rust formation begins. The corrosion which develops on laps and sheet edges of metal roofs compromises the metal's integrity and potentially cause leaks or structural damage if not treated.
- What Is Cut Edge Corrosion?
- What Causes Cut Edge Corrosion?
- How Do You Prevent Cut Edge Corrosion?
- What Happens If You Do Not Treat Cut Edge Corrosion?
- How Much Does Cut Edge Corrosion Treatment Cost?
- Frequently Asked Questions About Cut Edge Corrosion
- Our Cut Edge Corrosion Services
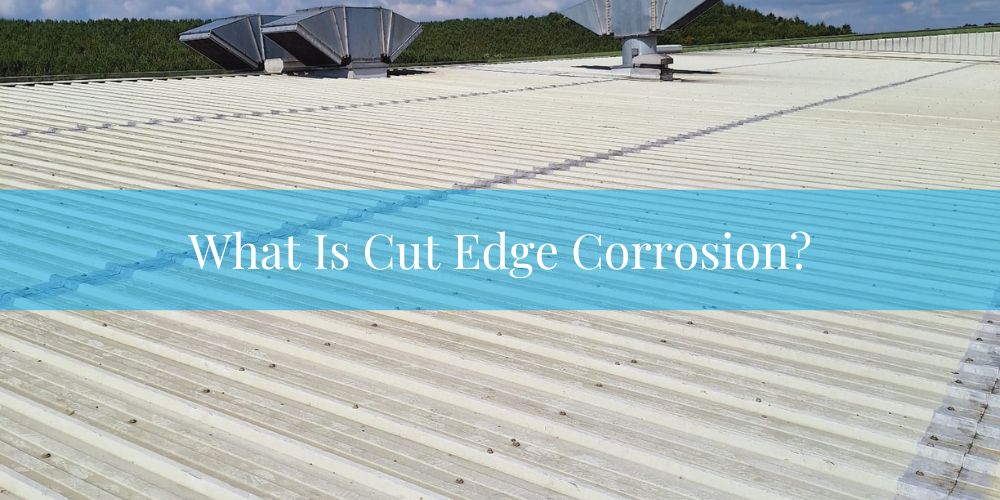
What Is Cut Edge Corrosion?
Cut edge corrosion is a specific form of degradation which occurs on the exposed edges of coated metal roofing and cladding materials, often where the protective coating has been cut or trimmed during installation. When these edges are left unprotected, they become vulnerable to environmental factors like moisture and air, leading to the oxidation of the underlying metal. Over time, this can result in rust formation, which not only disfigures the roof but also compromises its structural integrity. If left untreated, cut edge corrosion can lead to leaks, weakening of the metal, and ultimately, costly repairs or replacements.
In the UK, this issue is particularly prevalent due to the damp and variable climate, which accelerates the corrosion process. Effective treatment usually involves the application of specialised coatings which seal and protect the cut edge of metal roof panels to prevent further corrosion. Regular inspection, maintenance and prompt treatment are essential to reduce the risks associated with cut edge corrosion and prolonging the service life of industrial and commercial metal roofs.
Have a question about an upcoming project?
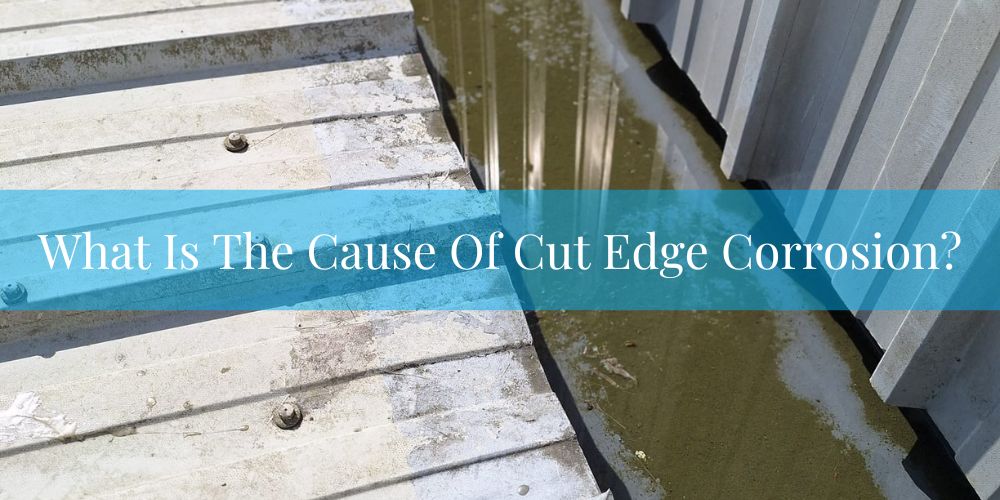
What Causes Cut Edge Corrosion?
The primary cause of cut edge corrosion is due to the exposure of unprotected metal edges which have been cut or sheared during the fabrication or installation of coated metal roofing and cladding systems. When these metal edges are severed, the protective coating which shields the metal surface is compromised, leaving the underlying metal exposed. The unprotected section of the metal roof panel is particularly susceptible to environmental elements, with moisture and oxygen being the primary catalysts in the oxidation process. When exposed to moisture, whether from rain, condensation, or high humidity the unprotected metal reacts with oxygen in the air. This leads to the formation of rust, most often in the form of edge peel. The corrosion process is significantly accelerated in environments rich in pollutants or salts, such as those found in coastal regions, where the corrosive nature of the atmosphere is intensified. Another cause of cut edge corrosion is galvanic corrosion. Galvanic corrosion is an electrochemical process in which two dissimilar metals in electrical contact degrade due to a conductive electrolyte, causing one metal (the anode) to corrode faster while the other (the cathode) remains protected.
Regardless of the cause of the corrosion, one the process has started, the rust spreads from the cut edges, potentially undermining the surrounding protective coating and exacerbating the corrosion process. Cut edge corrosion is a common issue in the UK, particularly in areas with high atmospheric pollution. In the UK, the mechanical stress caused by thermal expansion and contraction can lead to the development of micro-cracks along the cut edges, which create additional entry points for moisture. This cyclical stress, combined with constant exposure to harsh weather conditions, further accelerates the corrosion rate. If not addressed promptly, cut edge corrosion can lead to serious structural issues, including leaks, weakening of the metal, and ultimately necessitating costly repairs or even the replacement of the affected roofing components.
Regular inspections and timely maintenance are therefore essential to prevent the progression of cut edge corrosion and to preserve the integrity and longevity of metal roofing systems, particularly in the UK’s variable and often harsh climate.
- Exposure of Unprotected Metal Edges
- Moisture and Oxygen
- Pollutants and Salts
- Thermal Expansion and Contraction
- Mechanical Stress
- Inadequate Maintenance
1. Exposure of Unprotected Metal Edges
When coated metal roofing and cladding materials are cut or sheared during installation, the protective coating applied to the metal is often compromised, leaving the bare metal edges exposed to the environment. This exposure is critical because the protective coating, typically designed to shield the metal from corrosive elements, no longer provides coverage at the cut edges. As a result, these unprotected sections become highly susceptible to environmental factors, such as moisture and pollutants. This initial exposure is the primary cause of cut edge corrosion, which can rapidly lead to further deterioration if not promptly addressed.
2. Moisture and Oxygen
The combination of moisture and oxygen is the primary driver of the oxidation process, leading to rust formation on exposed metal edges. When rain, condensation, or humidity comes into contact with the unprotected metal, it reacts with the oxygen in the air to form iron oxide, commonly known as rust. This process is particularly prevalent in the UK’s damp climate, where high humidity levels are frequent. Rust formation begins almost immediately upon exposure to moisture and oxygen, initiating a cycle of corrosion that progressively weakens the metal structure if not properly managed.
3. Pollutants and Salts
In environments with high concentrations of pollutants or in coastal regions with salty air, the corrosive nature of the atmosphere is greatly intensified, which accelerates the cut edge corrosion process. Pollutants such as sulphur dioxide and chloride ions found in marine environments can exacerbate the rate of corrosion by penetrating the unprotected metal surface more aggressively. Coastal areas in the UK are particularly vulnerable to this form of accelerated corrosion, where the presence of saline particles in the air leads to quicker degradation of exposed metal surfaces.
4. Thermal Expansion and Contraction
The metal used in roofing and cladding undergoes expansion and contraction due to fluctuations in temperature. This thermal movement can cause micro-cracks along the cut edges, which further expose the metal to moisture ingress. These micro-cracks, though often invisible to the naked eye, provide additional pathways for water to penetrate, exacerbating the corrosion process. The cyclical nature of thermal expansion and contraction in the UK’s variable climate significantly contributes to the deterioration of metal roofing, especially at the cut edges where protection is minimal.
5. Mechanical Stress
Repeated mechanical stress, such as flexing, vibrations, or even wind loading, can increase the wear and tear on the exposed metal edges. Over time, these mechanical stresses can lead to the further breakdown of any remaining protective layers and deepen existing cracks, thereby accelerating the corrosion process. Industrial environments, where roofing and cladding systems are subject to continuous mechanical stress, are particularly at risk for accelerated cut edge corrosion if these factors are not adequately managed through proper design and maintenance.
6. Inadequate Maintenance
A lack of regular inspection and maintenance allows cut edge corrosion to go undetected and untreated, leading to more severe and widespread damage over time. Without routine maintenance, early signs of corrosion may be missed, allowing the rust to progress unchecked, eventually compromising the structural integrity of the metal roofing or cladding. Regular maintenance schedules be established, particularly in environments prone to high moisture or pollutant exposure, to identify and address signs of corrosion before they escalate into more significant issues. This proactive approach is essential for prolonging the lifespan of metal roofing systems and avoiding costly repairs or replacements.
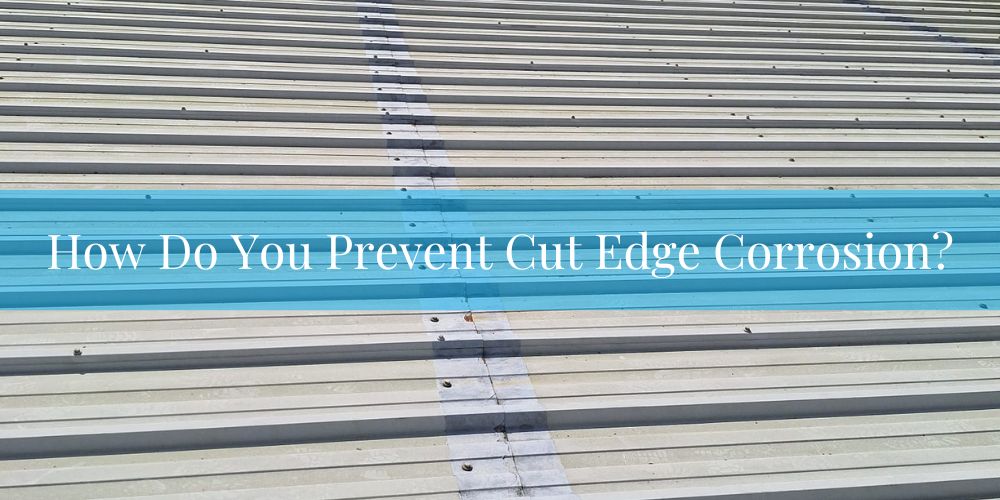
How Do You Prevent Cut Edge Corrosion?
To prevent cut edge corrosion, it is essential to apply specialised protective coatings, conduct regular inspections, and follow proper installation techniques. These coatings act as a barrier, safeguarding exposed metal edges from moisture and oxygen, which are the principal instigators of corrosion. Routine maintenance and inspections enable early identification of any issues, allowing for swift remediation or reapplication of coatings before substantial damage ensues. Employing proper installation techniques, including sealing cut edges immediately after they are made, further reduces exposure to corrosive agents. Additionally, selecting premium, corrosion-resistant materials and ensuring adequate drainage and ventilation can help avert moisture accumulation, thereby diminishing the likelihood of corrosion. Promptly addressing any signs of corrosion ensures that metal roofing and cladding systems remain resilient and functional over the long term. Below is a list of ways to prevent cut edge corrosion developing.
- Use of Protective Coatings
- Regular Inspections and Maintenance
- Proper Installation Techniques
- Selection of High-Quality Materials
- Avoiding Trapping Moisture
- Addressing Corrosion Quickly
1. Use of Protective Coatings
A highly effective method for preventing cut edge corrosion is the application of specialised protective coatings to the exposed edges of metal roofing and cladding. These coatings function as a defensive barrier, safeguarding the metal from environmental aggressors such as moisture and oxygen, which are principal culprits in the corrosion process. High-performance coatings, such as elastomeric or polymer-based formulations, are particularly advantageous due to their robust protective qualities and flexibility, allowing them to accommodate the thermal expansion and contraction inherent in metal structures. The prompt application of these protective coatings post-installation is essential for ensuring long-term durability. Modern coating technologies can significantly extend the lifespan of metal components by reducing the risk of corrosion at vulnerable edges.
2. Regular Inspections and Maintenance
Routine inspections and diligent maintenance are critical in identifying the early stages of cut edge corrosion and mitigating them before they develop into more severe issues. Regular scrutiny of the condition of metal roofing and cladding, especially at the edges where the protective coating might be compromised, facilitates timely intervention. Inspections should be conducted at least annually, with increased frequency in challenging environments such as coastal regions or industrial zones, where the risk of corrosion is heightened. Early detection not only enables maintenance teams to reapply protective coatings or perform minor repairs but also prevents the escalation of damage, which underscores the importance of proactive maintenance in extending the life of structural metal components.
3. Proper Installation Techniques
Adhering to proper installation techniques is paramount in reducing the risk of cut edge corrosion. During installation, it is crucial to minimise unnecessary cutting or shearing of the metal, as excessive handling can expose more of the underlying material to environmental elements than necessary. Immediately sealing the cut edges with protective treatments following cutting is an essential practice to prevent exposure to corrosive factors. Contractors are advised to follow best practices as prescribed by manufacturers and industry guidelines, to ensure that the risk of corrosion initiating at cut edges is significantly reduced. Moreover, ensuring the operatives who install the metal roofing system have corect training and certification for helps ensure there is adherence to these best practices.
4. Selection of High-Quality Materials
Selecting high-quality, corrosion-resistant materials for roofing and cladding is a pivotal strategy in preventing cut edge corrosion. Opting for materials with advanced protective coatings or those inherently resistant to corrosion, such as stainless steel or aluminium, ensures greater durability and an extended lifespan for the structure. The BRE advises that material selection should take into account the specific environmental conditions where the building is situated, as certain materials exhibit superior performance in particular climates. Additionally, research from the Steel Construction Institute (SCI) indicates that the use of high-grade materials not only reduces the incidence of cut edge corrosion but also offers better long-term economic benefits by decreasing maintenance costs and the need for premature replacements.
5. Avoiding Trapping Moisture
Designing and installing metal roofing and cladding systems to avoid trapping moisture is crucial in preventing cut edge corrosion. This involves ensuring that the roofing system has adequate drainage and ventilation to prevent water from pooling on the roof or becoming trapped in joints and seams. Moisture accumulation is a significant accelerant of corrosion, especially in areas where water can become trapped and continuously expose metal edges to damp conditions. Correct system design and installation is vital to avoid moisture entrapment and to extend the lifespan of metal cladding systems.
6. Addressing Corrosion Quickly
When cut edge corrosion is detected, it is imperative to address it swiftly to prevent further degradation. This process might involve cleaning the affected area, removing rust, and applying a new protective coating to halt the progression of corrosion. In more severe cases, replacing sections of the metal roofing or cladding may be necessary. Prompt cut edge corrosion repairs not only extend the life of the roofing system but also prevent more costly repairs or replacements in the future. Timely intervention is a key factor in preserving the integrity of building materials, and delaying repairs can exponentially increase restoration costs and the risk of structural failure.
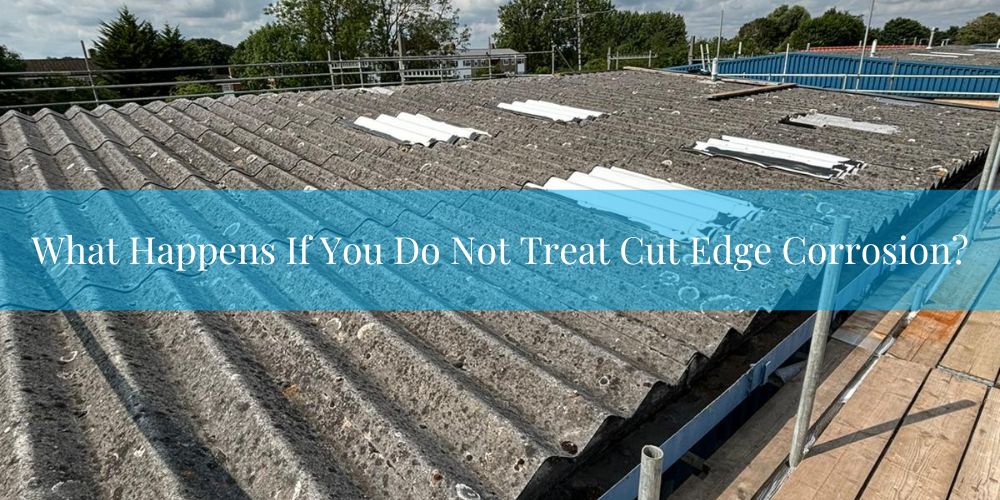
What Happens If You Do Not Treat Cut Edge Corrosion?
If you do not treat cut edge corrosion, it will progressively worsen, leading to structural deterioration, leaks, and increased repair costs. Once cut edge corrosion occurs, the corrosion will start to weaken the metal roof sheets. This will reduce the lifespan of the roofing system and potentially creating safety hazards. Additionally, untreated corrosion can decrease the property's value and contribute to environmental pollution due to the release of rust particles and the need for extensive repairs or replacements.
- Progressive Structural Deterioration
- Increased Risk of Leaks
- Escalating Repair Costs
- Reduced Lifespan of the Roofing System
- Potential Safety Hazards
- Decreased Property Value
- Environmental Impact
1. Progressive Structural Deterioration
Untreated cut edge corrosion will progressively worsen, leading to the gradual weakening of metal sheets in roofing or cladding systems. As rust spreads, it compromises the structural integrity of the metal, making it more vulnerable to environmental damage from wind, rain, and temperature fluctuations.This progressive deterioration can eventually result in significant structural failures, particularly in environments with harsh weather conditions.
2. Increased Risk of Leaks
As corrosion advances, it often leads to the formation of holes or gaps in the metal roofing or cladding. These breaches allow water to infiltrate the building, causing leaks that can severely damage interior elements, including insulation, electrical systems, and structural components. Water ingress due to untreated corrosion is a common cause of interior damage, leading to costly repairs and potential health hazards such as mould growth.
3. Escalating Repair Costs
The longer cut edge corrosion remains untreated, the more extensive and expensive the required repairs become. As corrosion spreads, larger portions of the roofing or cladding may need replacement. In severe cases, entire sections of the roof might need to be dismantled and rebuilt, which can be both costly and highly disruptive to building operations. Early intervention is crucial to avoid these escalating repair costs, as delayed maintenance can lead to exponential increases in repair expenses.
4. Reduced Lifespan of the Roofing System
Untreated corrosion significantly shortens the lifespan of metal roofing or cladding systems. What could have been a durable, long-lasting installation becomes a liability, necessitating early replacement much sooner than initially expected. Proactive management of corrosion issues is key to preserving the longevity of metal roofing systems, with untreated corrosion often leading to premature system failure.
5. Potential Safety Hazards
As corrosion weakens the metal structure, it can create serious safety hazards. Loose or compromised panels may pose risks to building occupants and visitors, particularly during high winds or severe weather events. In industrial settings, such deterioration can lead to non-compliance with safety regulations, potentially resulting in fines or legal consequences. Maintaining the integrity of building materials is essential for ensuring the safety of all users, with untreated corrosion being a significant safety concern.
6. Decreased Property Value
Industrial and commercial buildings affected by untreated cut edge corrosion are likely to experience a decline in property value. Visible signs of corrosion not only detract from the aesthetic appeal of a building but also signal underlying structural issues, which can deter potential buyers or investors. Properties with evident corrosion problems are often perceived as high-risk investments, leading to lower market values and reduced buyer interest.
7. Environmental Impact
Ignoring cut edge corrosion can also have negative environmental consequences. As metal deteriorates, rust particles and other contaminants may be released into the environment, contributing to pollution. Furthermore, the need for extensive repairs or replacements increases the demand for new materials, which in turn leads to greater resource consumption and waste generation. Sustainable building practices should include regular maintenance to prevent such environmental impacts, as untreated corrosion can exacerbate the ecological footprint of building operations
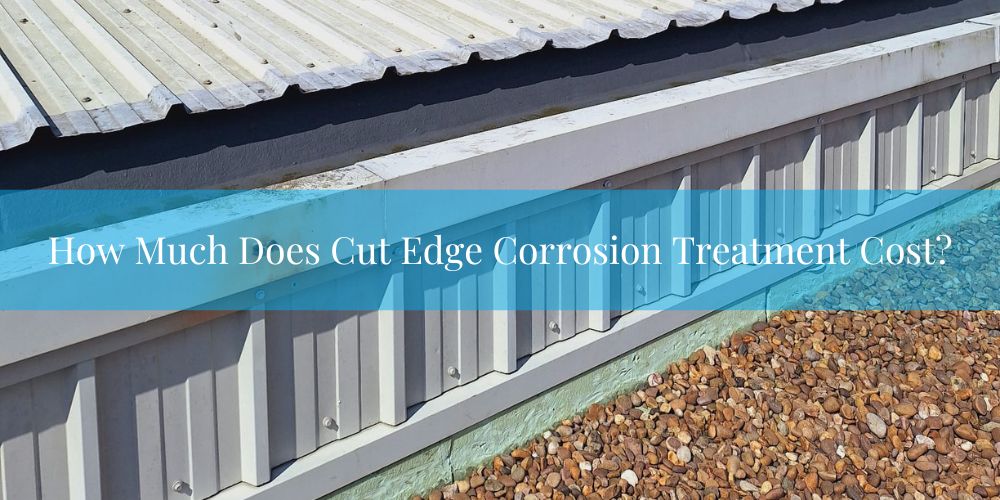
How Much Does Cut Edge Corrosion Treatment Cost?
Cut edge corrosion treatment costs between £54 and £125 per linear metre. The cost of treating cut edge corrosion is influenced by factors such as the size and severity of the affected area, the type of materials used, access and height challenges, location, labour rates, and environmental conditions. Additional considerations include regulatory requirements and the urgency of the project.
Service | Cost Range |
---|---|
Cut Edge Corrosion Treatment | £54 to £125 per linear metre |
*These estimates are advisory. Actual costs can vary based on specific project requirements, location, and market conditions.